
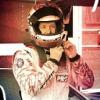





Cage ain't easy, but it's necessary
Posted by
Adax
,
06-07-2013
·
3,647 views
Building a cage is much more stressful than I anticipated. In retrospect, it's nice to step back at the end of the day and admire what you've created from a bunch of straight tubes, but I found I needed a mental break from the fabrication process every 2 hours or so. It's not all that difficult in concept, the math is straightforward but the three dimensional aspect can surprise you occasionally. DOM tubing is not cheap either so the financial pressure is there as well.
Working with round tubing is different from square, due to notched fitment. It's possible to end up needing to place a tube somewhere that is physically impossible so you have to plan several steps ahead. For instance, imagine a square constructed of round tube. Say you want to place a diagonal inside the square, from one corner to the other. Due to having to notch the ends of the diagonal, it cannot be done. This type thing often results in you not knowing if a piece will fit correctly until is has been irreversibly bent and notched.
Tubing: 1.5" diameter (outer, tubing is spec'd by OD, pipe by ID) 0.095" wall thickness DOM (Drawn Over Mandrel) tubing fits the rules and is the most commonly used in SM cages. Thinner wall may be used in the non-required components of the cage for weight savings. I went with 0.065" wall thickness for these areas which saves more weight than you might think. I'll double check but I think I found a foot of 0.095" to weight 1 pound and a foot of 0.065" to weight 0.6 pounds. I went with 3/16' plate for mounting points. The best (cheapest) place I found to purchase tubing was Marmon/Keystone. They are located in most major cities and will sell to the public. There is a major price break if you purchase at least 100 pounds so keep this in mind. They don't sell sheet/plate so you'll need to source this elsewhere. I used the online supplier MetalsDepot with no complaints. You can easily build the minimum cage required by the GCR with 100 ft of tubing. I used around 120.
Tools: You can cut tubing with a Sawzall or a cut-off wheel but for the number of cuts a full cage will require, a chop saw is worth every penny. I bought a Hitachi one for around $100 at Lowes and it held up well. Next you need a bender and a notcher. I can't say enough good things about JD Squared benders and notchers. In addition to being based in my home town, the quality is amazing for the price. I don't think I could purchase the amount of materials required to build one myself for what one costs. I went with a Model 3 bender which was more than adequate and is precise down to 1 degree. I bought the smallest radius die, I could not think of a reason for a larger diameter die. I used their Notchmaster for notches. I went through 3 hole-saws but I cut at least 100 notches and often did not bother with cutting lube. Occasionally I wished for a notcher that would let me cut notches in a bend like The Beast but I'm not sure I could justify the price (and size of the thing). Keep in mind which angle you are setting the notcher. You often need the complimentary angle (90 minus the angle you measured). The notcher has 0 degrees as perpendicular to the tube. I usually measured with 0 degrees as parallel to the tube. That and an angle grinder and you are set.

Oh, you'll need a welder too. I don't know enough about welding to make an informed recommendation but I've been happy with my my Miller 211. MIG welding a cage is fine (and may be preferred) but it can't compare with TIG in aesthetics. Avoid flux-core welding for something this important. I also have a Hypertherm Powermax 30 Plasma Cutter and it may be my favorite tool in the shop.It's Carrie Byron's favorite as well. Like my lift, I don't know how I ever survived without it.

Now a bit about cage design. There are as many opinions about SM cage design as there are cages. Don't believe me, find two exactly alike. I put a lot of thought into the design of my cage, and leaned on the experience of others like Dan Tiley. In the end I'm happy with what I built. doing it over, there are things I would probably do differently, but it complies with the rules and achieves my design goals.
I played around a bit with some of the bend software packages (the free ones) but in the end I found it easier to do it manually. I wasted 6 feet of tube on the green Miata's main hoop using a software derived bending plan. I used a digital angle finder, tape measure, scientific calculator, and a sharpie for the entire cage. A basic knowledge of trig helped as well. Key to planning bends is a bend template. Sacrifice about 2 feet of tubing to make a 90 degree bend, marking the template to correspond with a repeatable reference point on the bending die. Bends do not start at the end of the die so to plan bends, having an exact pattern of both the bend start point and the bend radius (outer usually) is essential.
Working with round tubing is different from square, due to notched fitment. It's possible to end up needing to place a tube somewhere that is physically impossible so you have to plan several steps ahead. For instance, imagine a square constructed of round tube. Say you want to place a diagonal inside the square, from one corner to the other. Due to having to notch the ends of the diagonal, it cannot be done. This type thing often results in you not knowing if a piece will fit correctly until is has been irreversibly bent and notched.
Tubing: 1.5" diameter (outer, tubing is spec'd by OD, pipe by ID) 0.095" wall thickness DOM (Drawn Over Mandrel) tubing fits the rules and is the most commonly used in SM cages. Thinner wall may be used in the non-required components of the cage for weight savings. I went with 0.065" wall thickness for these areas which saves more weight than you might think. I'll double check but I think I found a foot of 0.095" to weight 1 pound and a foot of 0.065" to weight 0.6 pounds. I went with 3/16' plate for mounting points. The best (cheapest) place I found to purchase tubing was Marmon/Keystone. They are located in most major cities and will sell to the public. There is a major price break if you purchase at least 100 pounds so keep this in mind. They don't sell sheet/plate so you'll need to source this elsewhere. I used the online supplier MetalsDepot with no complaints. You can easily build the minimum cage required by the GCR with 100 ft of tubing. I used around 120.
Tools: You can cut tubing with a Sawzall or a cut-off wheel but for the number of cuts a full cage will require, a chop saw is worth every penny. I bought a Hitachi one for around $100 at Lowes and it held up well. Next you need a bender and a notcher. I can't say enough good things about JD Squared benders and notchers. In addition to being based in my home town, the quality is amazing for the price. I don't think I could purchase the amount of materials required to build one myself for what one costs. I went with a Model 3 bender which was more than adequate and is precise down to 1 degree. I bought the smallest radius die, I could not think of a reason for a larger diameter die. I used their Notchmaster for notches. I went through 3 hole-saws but I cut at least 100 notches and often did not bother with cutting lube. Occasionally I wished for a notcher that would let me cut notches in a bend like The Beast but I'm not sure I could justify the price (and size of the thing). Keep in mind which angle you are setting the notcher. You often need the complimentary angle (90 minus the angle you measured). The notcher has 0 degrees as perpendicular to the tube. I usually measured with 0 degrees as parallel to the tube. That and an angle grinder and you are set.
Oh, you'll need a welder too. I don't know enough about welding to make an informed recommendation but I've been happy with my my Miller 211. MIG welding a cage is fine (and may be preferred) but it can't compare with TIG in aesthetics. Avoid flux-core welding for something this important. I also have a Hypertherm Powermax 30 Plasma Cutter and it may be my favorite tool in the shop.It's Carrie Byron's favorite as well. Like my lift, I don't know how I ever survived without it.

Now a bit about cage design. There are as many opinions about SM cage design as there are cages. Don't believe me, find two exactly alike. I put a lot of thought into the design of my cage, and leaned on the experience of others like Dan Tiley. In the end I'm happy with what I built. doing it over, there are things I would probably do differently, but it complies with the rules and achieves my design goals.
I played around a bit with some of the bend software packages (the free ones) but in the end I found it easier to do it manually. I wasted 6 feet of tube on the green Miata's main hoop using a software derived bending plan. I used a digital angle finder, tape measure, scientific calculator, and a sharpie for the entire cage. A basic knowledge of trig helped as well. Key to planning bends is a bend template. Sacrifice about 2 feet of tubing to make a 90 degree bend, marking the template to correspond with a repeatable reference point on the bending die. Bends do not start at the end of the die so to plan bends, having an exact pattern of both the bend start point and the bend radius (outer usually) is essential.
