
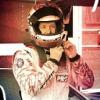





Package Tray
Posted by
Adax
,
06-23-2013
·
3,027 views
Several vendors sell an aluminum package tray cover kit like this:

To my knowledge, the only company making these is AWR, and even they sub out the laser cutting and bending. I mention this because depending upon when you decided to purchase one of these, you may be waiting several months for another production run. I waited 4 and it held up my build significantly because I could not complete the cage until the tray was in. The rules require that the rear bulkhead be sealed to completely separate the fuel tank from the driver. This is a more elegant and likely more effective method than the 32g aluminum tape that is common.
Delays aside, this is a very nice kit. I'm told AWR used to sell these, and other trick Mazda parts, directly to Mazdaspeed. Even though I had to cut mine up significantly as it is not designed for a package shelf main-hoop mount, it is difficult to see any area that could be improved upon.
You have to, of course, cut holes in the appropriate locations for your rear tubes and rivet the thing together. I made cardboard templates of the main pieces to determine where the holes needed to be cut. Some luck is involved as the tubes can only be taped into position, otherwise the pieces cannot be moved in and out. Here's one of the templates.

It's easier to cut a big hole in the main template and tape smaller pieces to it to more precisely determine the cut locations, like this:

Once I was happy, I traced the shape and locations of the cuts to the aluminum pieces and got the plasma cutter out. I seriously hoped I was not cutting this piece I waited 4 months for in the wrong place, I was reasonably happy with the results.

The kit comes with a center piece to allow access to the fuel pump, but no means of attaching this piece. Sheet metal screws would probably suffice but I wanted something a little more professional. I ordered some quarter-turn fasteners for the job, and quite a job it was. First the location of the fasteners is determined and holes drilled.

It helps to dimple the holes in order to get the fasteners to fit nicely. I purchased a set of dimple dies a few years ago and one of them fit perfectly.

Now the fasteners can be riveted into place.

They need to be fastened to something though and since there is only 0.5" overlap of the cover panel with the main pieces some sort of bracket must be used. Weld-brackets can be purchased from the same places that sell the fasteners, and I have some, but they did not fit well and were going to require so much modification that I thought it would be faster to just make my own. Here are the brackets before cutting and after drilling. A surprising number of holes are needed for all the rivets and rivet avoidance. A CNC plasma cutter table would be so nice for this but it's too hard for me to justify the cost of one of these.

The little capture wires are then riveted to the brackets. Attach all brackets to the cover, position the cover, then drill/rivet the brackets to the main pieces, winding up with this when viewed from underneath.


To my knowledge, the only company making these is AWR, and even they sub out the laser cutting and bending. I mention this because depending upon when you decided to purchase one of these, you may be waiting several months for another production run. I waited 4 and it held up my build significantly because I could not complete the cage until the tray was in. The rules require that the rear bulkhead be sealed to completely separate the fuel tank from the driver. This is a more elegant and likely more effective method than the 32g aluminum tape that is common.
Delays aside, this is a very nice kit. I'm told AWR used to sell these, and other trick Mazda parts, directly to Mazdaspeed. Even though I had to cut mine up significantly as it is not designed for a package shelf main-hoop mount, it is difficult to see any area that could be improved upon.
You have to, of course, cut holes in the appropriate locations for your rear tubes and rivet the thing together. I made cardboard templates of the main pieces to determine where the holes needed to be cut. Some luck is involved as the tubes can only be taped into position, otherwise the pieces cannot be moved in and out. Here's one of the templates.
It's easier to cut a big hole in the main template and tape smaller pieces to it to more precisely determine the cut locations, like this:
Once I was happy, I traced the shape and locations of the cuts to the aluminum pieces and got the plasma cutter out. I seriously hoped I was not cutting this piece I waited 4 months for in the wrong place, I was reasonably happy with the results.
The kit comes with a center piece to allow access to the fuel pump, but no means of attaching this piece. Sheet metal screws would probably suffice but I wanted something a little more professional. I ordered some quarter-turn fasteners for the job, and quite a job it was. First the location of the fasteners is determined and holes drilled.
It helps to dimple the holes in order to get the fasteners to fit nicely. I purchased a set of dimple dies a few years ago and one of them fit perfectly.
Now the fasteners can be riveted into place.
They need to be fastened to something though and since there is only 0.5" overlap of the cover panel with the main pieces some sort of bracket must be used. Weld-brackets can be purchased from the same places that sell the fasteners, and I have some, but they did not fit well and were going to require so much modification that I thought it would be faster to just make my own. Here are the brackets before cutting and after drilling. A surprising number of holes are needed for all the rivets and rivet avoidance. A CNC plasma cutter table would be so nice for this but it's too hard for me to justify the cost of one of these.
The little capture wires are then riveted to the brackets. Attach all brackets to the cover, position the cover, then drill/rivet the brackets to the main pieces, winding up with this when viewed from underneath.