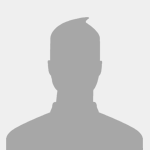
Question about NB diff pinion crush sleeve
#1
Posted 02-08-2022 11:17 PM



#2
Posted 02-09-2022 10:51 AM

Zero expertise but I can say I've seen several desperate in the paddock attempts to remove a loose counter weight. The nut was marked and put back in the exact same position. Both times the repair seemed to hold at least that weekend!
My personal method has never failed for this repair...though your safety should be considered! 4" grinder with the thinest cut off wheel. If wheel is half worn out it it better(radius)! Pin the loose weight so it wont move...lay grinder wheel at a 45 degrees across the shallow area and carefully cut until the blade touches or is about to touch the pumpkin and outer flange. You will not be all the way thru the metal but close. Do the same thing on the opposite side(180 degrees). After both sides have been cut use a hammer and cold chisel to break the remaining metal on one or both sides...it comes right off! Successfully done this under the car in the paddock BUT on the bench or the lift is a lot more comfortable
I realize this doesnt answer/solve your situation Steve...sorry! Advise for others who dont want to find themselves in your position
Ron
RAmotorsports


#3
Posted 02-09-2022 02:49 PM

Many times I've taken the pinion flange off ( seal, etc..) whether for a Chevy, Miata,etc..., I've always marked and run back up with an impact back to the mark, but even if I wasn't watching the mark, as long as I wasn't letting the impact rip ( just let the gun do a couple "ugga-duggas") it always went back to pretty much where it started. It takes a lot of torque to get crush sleeves to crush.
#4
Posted 02-25-2022 05:45 PM

Steve,
There are several approaches that you can use to allow you to re-use a crush sleeve.
I would recommend doing this on a bench with the diff out of the vehicle, but it can also be done with the diff in the car. If doing it in the car, I would also recommend disengaging the half shafts as the loads from the CV joints as well as articulation loads from the half-shaft will make getting accurate preload "drag" measurements difficult and likely highly suspect.
Next is to document the torque required to turn of the diff pinion flange. Use an 'in. - lb." dial or beam torque wrench, before disturbing the pinion nut. After getting the pre disassembly torque reading you can then mark the pinion nut and flange as assembled so it can be reassembled in the same alignment as original.
When it is time, reassemble the pinion flange on the original pinion shaft at the original spine orientation. At this point you would then tighten the pinion nut to where it approaches the original marked position on the pinion shaft. At that point start checking the torque to turn for the pinion shaft. Continue to tighten the pinion nut until it reads at least 5-to-10-inch pounds higher than what was measured when dis-assembled. If you are replacing the front seal, bearing and/or outer race, you should expect to see a higher pinion torque to turn than when using all original parts, but I would not expect to tighten the pinion nut to a point greater than 30-to-35-inch pounds turning torque.
In situations where no torque to turn measurements were obtained or marking of the assembly orientation was not done, it is still possible to re-use the crush sleeve assuming the diff was just disassembled from its original factory set-up and the crush sleeve was not overly crushed by a gorilla with 1000 ft-lb impact gun. The trick here is to just slowly creep up while re-installing the pinion nut so you are sure you are seating the bearings in the cups while removing all play. Check the rotating torque early and often as you tighten the nut, looking to see the pinion torque just begin to register in the 5-to-10-inch pound range. Then continue to tighten looking for a slow and consistent increase in the level of torque required to turn the pinion flange. Under this situation I would definitely use the 30 to 35 inch-pound "torque to turn" level whereas you might only be using 15-20 inch-pounds of torque where you captured the data ahead of time.
Another option where you may need a new crush sleeve but not have access to one is to visit a local differential service shop where you should be able to find a selection of small pinion shims that you could place between either the top or bottom of the crush sleeve and bearings. You are in effect just creating a longer crush sleeve with the use of shims as the original sleeve will be able to continue to compress given the new overall height gained from the repurposed shims. I would suggest looking at Dana 30 Jeep front axles as a potential start.
It should be noted that when working on differentials, you should never tighten the pinion nut using a torque value. When collapsing a crush sleeve, you typically reach the highest tightening torque prior to the crush sleeve being compressed to the appropriate height required for the desired bearing preload. What would likely happen when tightening to a specified torque is the torque value would be reached before the crush sleeve is properly compressed and the front pinion bearings would be loose in the bearing cups.
#5
Posted 02-26-2022 11:36 PM

Then it was time to reinstall the ring gear and Torsen, and set the ring & pinion backlash which is a very simple process EXCEPT that the factory manuals have a misprint in a critical step. I checked earlier and later models and the same misprint exists through at least 2005, which honestly shocked me. It says to mark teeth at 90 degree intervals and adjust backlash until one is between 0.09-0.11 mm. So far so good, but then it says check the OTHER THREE and make sure the Maximum is LESS than 0.07. Clearly that makes NO sense. The first couple times I read through it quickly just for an overview my mind must have substituted “minimum not less than” or the equivalent but when I actually did each step I read it again carefully and realized what it really said. Then it struck me that my subconscious substitution doesn’t work either because it fails to define an upper limit, which can’t be right. That stopped me cold until I had time to do more digging and found similar instructions for other diffs. In the end this is what I believe is correct. Though a bit convoluted it does define an absolute minimum and backs into a relative maximum:
After adjusting lash on the first marked tooth to 0.09-0.11 mm, inspect the backlash at the three other marked points and make sure that the minimum backlash is more than 0.05 mm and the difference of the maximum and minimum backlash value is less than 0.07 mm. I kept doubting myself wondering how the heck such an error could get copied year after year without someone in the field calling their attention to it, but most of the people I’ve talked to who work on them do most of it by “feel”. But it’s still a bit surprising. If someone thinks I’ve got it wrong, please explain.

The last step is setting the side bearing preload which is achieved not with a torque or resistance value but rather physical measurements between machined surfaces on the bearing caps. That required adding a new tool to my box and was initially a bit counterintuitive because tightening the adjusters (increasing preload) forces the towers/caps to spread further apart, but then it went fine if a bit tedious not knowing how much adjustment was needed while also keeping the lash in-spec.
I swore off messing with diffs 40+ years ago. Who says the young are stupid?

- RWP80000 and lillyweld like this


#6
Posted 02-28-2022 08:26 AM

my experience setting backlash is that the first thing i did when i bought the tools to do it, was go through my stack of working, used diffs, and measure them.
literally none of them met spec. this was a stack of 3 or 4 used open and LSD stock diffs. probably due to wear of some type. but it does mean that your diff will work, sound fine, transfer power, and last a while, even if its outside spec. when i set up diffs now, i do hit the spec. but its also comforting to know there is some wiggle room.
i use this table of specs:
https://www.miata.ne...ge/diff_rr.html
- Steve Scheifler likes this
Gordon Kuhnley: Driving miata's in all conditions, courses, and motorsports that I can.
#7
Posted 02-28-2022 10:52 PM

my experience setting backlash is that the first thing i did when i bought the tools to do it, was go through my stack of working, used diffs, and measure them.
literally none of them met spec. this was a stack of 3 or 4 used open and LSD stock diffs. probably due to wear of some type. but it does mean that your diff will work, sound fine, transfer power, and last a while, even if its outside spec. when i set up diffs now, i do hit the spec. but its also comforting to know there is some wiggle room.
i use this table of specs:
https://www.miata.ne...ge/diff_rr.html
Mostly seems about right but his ring/pinion backlash is definitely incorrect, even more so than the manual. If you can get there, excellent, but it’s WAY more restrictive than it should be and could very easily lead someone to believe their diff isn’t salvageable.


#8
Posted 03-01-2022 12:01 PM

Mostly seems about right but his ring/pinion backlash is definitely incorrect, even more so than the manual. If you can get there, excellent, but it’s WAY more restrictive than it should be and could very easily lead someone to believe their diff isn’t salvageable.
what is the backlash spec in the manual? converting .09-.11mm is 3.5-4.3mils. looks right to me.
Gordon Kuhnley: Driving miata's in all conditions, courses, and motorsports that I can.
#9
Posted 03-01-2022 09:55 PM

what is the backlash spec in the manual? converting .09-.11mm is 3.5-4.3mils. looks right to me.
Did you read my post above? That’s the STARTING point, effectively the middle of the allowed range. The manuals are right to that point then absolutely miss-worded as I explained above. The allowed range from max of four measurements to min of those four is 0.07mm, whereas .09-.11 mm is far narrower.


#10
Posted 03-01-2022 10:56 PM



#11
Posted 03-02-2022 07:48 AM

If you work through how the spec is supposed to be worded, the total acceptable range is actually 0.05mm at the minimum and 0.18mm at the max BUT a given diff should have a min-max variance of no more than 0.07mm. Like I said, very different from several versions of the FSM and dramatically different than the linked how-to.
so thats .002"- .007" as tolerance for any single measurement, but the range on any single diff should be less than .0027"
interesting.
ive seen them run silent and be workable with over .013" but yeah, i get them in the 3-4mil range typically before i run them.
Gordon Kuhnley: Driving miata's in all conditions, courses, and motorsports that I can.
0 user(s) are reading this topic
0 members, 0 guests, 0 anonymous users