
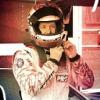





Carbon fiber work
Posted by
Adax
,
07-01-2013
·
3,862 views
As some may know, I spent way to much time a couple of years ago covering my 1.6's dash pieces with 3M Dinoc and Alcantara.
Forum Thread
The Alcantara is great but the Dinoc, while looking better than 23 year old dash plastic, would never be mistaken for real carbon fiber. I wanted to go with the Alcantara covering again as it's pretty simple and helps with glare (FWIW) but I wanted an alternative to the Dinoc. I wasn't able to find anyone making replacement carbon fiber dash pieces for Miatas, and they wouldn't be legal anyway. I looked into covering the existing pieces with carbon fiber and came across these guys.
www.carbonmods.com
Turns out what I wanted to do can be done and it's called Skinning. I ordered a medium kit and after much frustration getting hazardous materials shipped from the UK, promptly made a huge mess of a plastic Miata steering shaft/ignition cover. Skinning is difficult as I soon learned and the pieces they use in the videos are selected for their shape. I practiced on some wheel well trim pieces as they have complex curves with slowly improving success. I needed a more reasonable source of materials and found Fiber Glast based on the recommendation of a composite forum. They are top-notch. Great products and service at a very reasonable price.
I tried my hand at vacuum bagging to get the fabric to mold better to complex surfaces with mixed results. Vacuum bagging works well for making CF parts in a mold but it was never intended for sticking CF sheets to existing pieces for a variety of reasons I slowly discovered. PM me if you even care.
Once the general technique was perfected on random stuff in the garage, it was time to start on some dash pieces. I've found over the years that if I could do a project a second time, I could do a far better job due to the knowledge gained the first time. I decided it was probably worth doing this one twice. It would cost an additional $200 in materials but hopefully it would pay off. If the first attempt turned out perfect, all the better.
Here's a big roll of carbon fiber in the kitchen. Even if this stuff was as cheap and common as newsprint it would still look exotic.

The flattest surface is probably the top of the dash by the windscreen so that's where I started. The challenge here is the defroster vents. I cut out the "braces" leaving two large vents which should be easier to deal with. First step is to cover the dash with epoxy, let it set until tacky, then apply the fabric.

The fabric contours well. The key to working with this stuff is patience and timing. The base layer must be completely hardened before applying any more epoxy or it will separate. Once set, I usually use 3M medium upholstery adhesive to secure the corners and back-sides to the piece. Then its a matter of multiple layers of epoxy (usually 4). Its behavior depends on temperature and humidity. Epoxy resin is much more sensitive than polyester resins which I've used on fiberglass projects. The mix ratio must be exact so I used a small postal scale.
Here is the piece after 4 layers of epoxy.

Once hardened, it must be sanded flat and wet sanded until smooth. You can see it is not contouring well to the defrost vents and I actually cut this one shorter than I needed to for the cage so this one is going in the discard bin.
Forum Thread
The Alcantara is great but the Dinoc, while looking better than 23 year old dash plastic, would never be mistaken for real carbon fiber. I wanted to go with the Alcantara covering again as it's pretty simple and helps with glare (FWIW) but I wanted an alternative to the Dinoc. I wasn't able to find anyone making replacement carbon fiber dash pieces for Miatas, and they wouldn't be legal anyway. I looked into covering the existing pieces with carbon fiber and came across these guys.
www.carbonmods.com
Turns out what I wanted to do can be done and it's called Skinning. I ordered a medium kit and after much frustration getting hazardous materials shipped from the UK, promptly made a huge mess of a plastic Miata steering shaft/ignition cover. Skinning is difficult as I soon learned and the pieces they use in the videos are selected for their shape. I practiced on some wheel well trim pieces as they have complex curves with slowly improving success. I needed a more reasonable source of materials and found Fiber Glast based on the recommendation of a composite forum. They are top-notch. Great products and service at a very reasonable price.
I tried my hand at vacuum bagging to get the fabric to mold better to complex surfaces with mixed results. Vacuum bagging works well for making CF parts in a mold but it was never intended for sticking CF sheets to existing pieces for a variety of reasons I slowly discovered. PM me if you even care.
Once the general technique was perfected on random stuff in the garage, it was time to start on some dash pieces. I've found over the years that if I could do a project a second time, I could do a far better job due to the knowledge gained the first time. I decided it was probably worth doing this one twice. It would cost an additional $200 in materials but hopefully it would pay off. If the first attempt turned out perfect, all the better.
Here's a big roll of carbon fiber in the kitchen. Even if this stuff was as cheap and common as newsprint it would still look exotic.
The flattest surface is probably the top of the dash by the windscreen so that's where I started. The challenge here is the defroster vents. I cut out the "braces" leaving two large vents which should be easier to deal with. First step is to cover the dash with epoxy, let it set until tacky, then apply the fabric.
The fabric contours well. The key to working with this stuff is patience and timing. The base layer must be completely hardened before applying any more epoxy or it will separate. Once set, I usually use 3M medium upholstery adhesive to secure the corners and back-sides to the piece. Then its a matter of multiple layers of epoxy (usually 4). Its behavior depends on temperature and humidity. Epoxy resin is much more sensitive than polyester resins which I've used on fiberglass projects. The mix ratio must be exact so I used a small postal scale.
Here is the piece after 4 layers of epoxy.
Once hardened, it must be sanded flat and wet sanded until smooth. You can see it is not contouring well to the defrost vents and I actually cut this one shorter than I needed to for the cage so this one is going in the discard bin.